How do REDARC test their products?
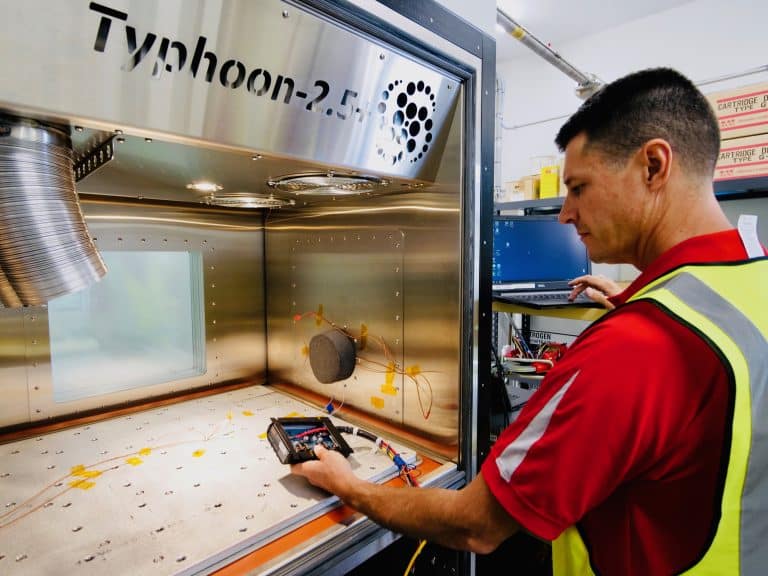
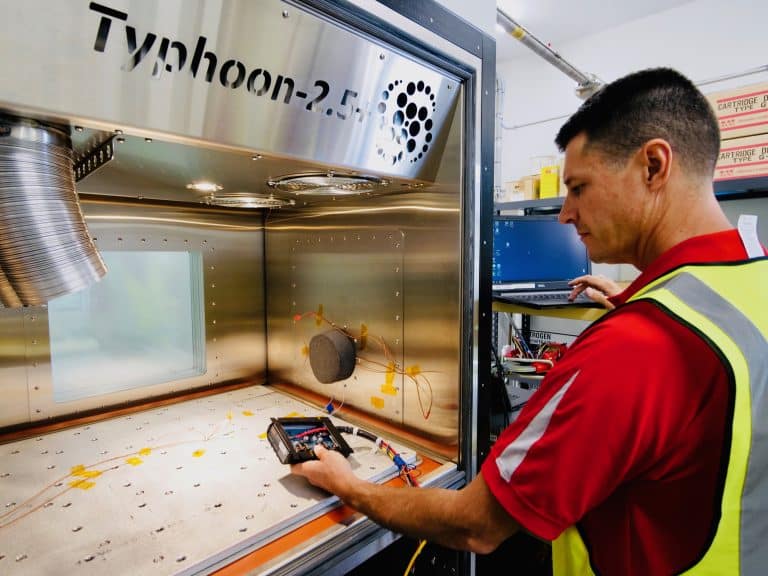
Ever wondered how REDARC products are tested before they hit the market?
When investing your hard-earned dollars into outdoor gear, it’s reassuring to know it’s going to last the distance. After all, quality products should come with quality assurance. That’s why one brand in particular, REDARC, takes product testing seriously. To ensure reliability and performance, REDARC has state-of-the-art Test & Validation Laboratories that effectively evaluate compliance and reliability.
We wanted to delve into this a little further to discover just what sets REDARC apart and how they ensure their products do as they say they will.
The EMC Laboratory stands for electromagnetic compatibility. This lab allows REDARC to ensure that their products are compliant in terms of Radio Frequency (RF) emissions and immunity. Products are required to have low RF emissions. This ensures that they don’t affect other nearby devices. A high level of immunity is also important to ensure the products themselves are unaffected when they’re used in a RF rich environment. An RF rich environment may be near mobile phones or when you’re driving by TV transmission towers.
Off-road conditions can cause vibration. This is why REDARC conduct vibration testing to ensure their products will be able to operate and survive vibration. They do this by exposing the products to vibration and temperature extremes. Also known as this ‘shake and bake’ testing, this emulates a lifetime of real-life conditions. It ensures REDARC products are testing against the harsh vibration and temperatures they may face when they’re installed in off-road vehicles, to give you peace of mind.
It works by utilising a Shaker/Environmental Chamber combination referred to as AGREE. This stands for Advisory Group for the Reliability of Electronic Equipment. This way of testing combines a single axis electromagnetic shaker with an environmental chamber. This is what enables products to be subjected to accelerated vibration profiles whilst simultaneously being exposed to hot, cold and humidity environmental cycles.
Why are products exposed to more severe levels than they ever will be in reality? Well, that’s how one or two weeks of testing in the lab can correspond to many years of use. Rather than hold products hostage for years on end for testing, the process is accelerated.
REDARC also use a HALT Chamber, which refers to Highly Accelerated Life Testing. HALT testing allows REDARC’s engineers to stress products to the point of failure. They do this by using rapid thermal changes and random vibration. Weak points are therefore identified and improved to ensure that any weaknesses are designed out of the final product and never reach the customer.
In the test and validation laboratories, you’ll find a team with a diverse range of skills and experience. Some of them have backgrounds in electronics, others engineering. Some have backgrounds in mechanical engineering, others industrial chemistry and EMC and compliance specialists. There are even recent graduates and students who are working on final year projects. REDARC’s testing is therefore performed by a range of people who have many years of combined industrial experience.
Knowing your product has been pressure tested before even hitting the market allows an increased sense of trust in your purchase. It’s also reassuring to hear just how extensive the testing process is on REDARC’s behalf, so you know you’re buying an item that has been carefully designed and executed.